DUBAI, UAE / ACCESS Newswire / July 18, 2025 / In an effort to increase efficiency and consistency across its vast network of fuel stations, convenience stores, and food outlets, EG Group has partnered with flowdit to digitize frontline operations. The result: a 20% reduction in process time, enhanced transparency, and real-time issue resolution across thousands of locations worldwide.
Learn more about this project and other use cases at: https://flowdit.com/case-studies
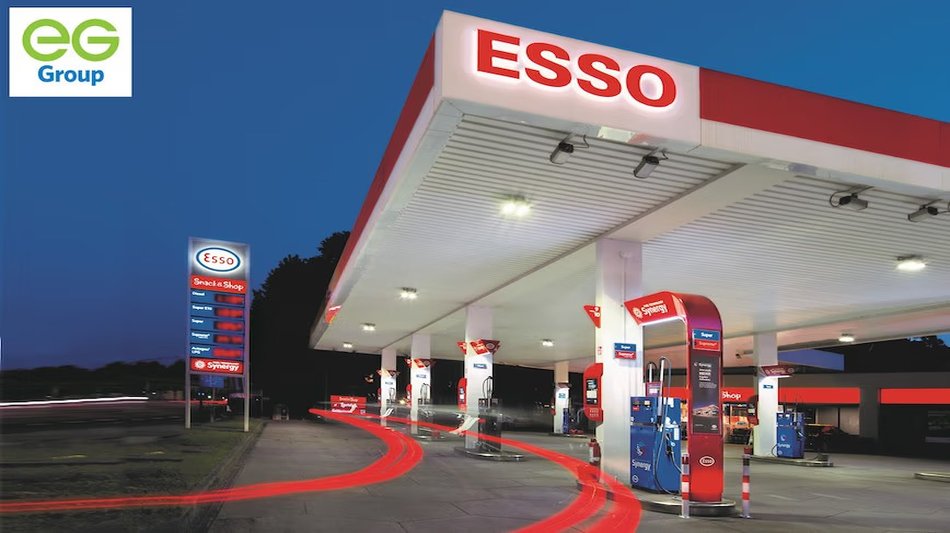
Tackling Complexity Across a Global Network
Operating thousands of branded sites across Europe, North America, and Asia-Pacific, EG Group faced a common challenge: fragmented, paper-based processes that slowed down decision-making, introduced errors, and made it difficult to enforce consistent operational standards.
Each site, whether a SPAR convenience store, Esso fuel station, or KFC restaurant, had its own procedures. Manual checklists created delays, duplicated efforts, and placed a significant burden on site managers and regional supervisors. Audit preparation was time-consuming, compliance reporting inconsistent, and management visibility limited to retrospective summaries rather than real-time insights.
This fragmentation not only hindered operational performance, but also limited the organization's ability to scale best practices and respond quickly to on-the-ground issues.
The Solution: A Real-Time Connected Operations Platform
EG Group introduced flowdit, a Connected Operations Platform designed to digitize, unify, and streamline frontline workflows. The platform replaced paper and spreadsheets with intuitive digital tools that guide, document, and escalate operational tasks as they happen.
Key capabilities include:
Step-by-step digital inspections to ensure accuracy and reduce ambiguity across teams and regions
Automated task assignments triggered by deviations, enabling immediate corrective action
Centralized dashboards showing live data trends, recurring issues, and key performance indicators
Audit-ready digital records with tamper-proof time and user stamps, ensuring regulatory compliance at all times
These tools empower teams to act in real time, while giving management the oversight needed to monitor performance and make data-informed decisions across a highly distributed network.
Measurable Results Across Operations
Since implementing flowdit, EG Group has seen tangible improvements in both speed and quality of execution:
20% reduction in process execution time, achieved by eliminating manual steps, redundant paperwork, and unnecessary follow-up calls
Faster resolution of issues, driven by real-time alerts and centralized visibility
Higher frontline engagement, as staff contributions are now directly tied to measurable impact
Greater consistency across sites, with digital checklists enforcing corporate standards
Streamlined audits, supported by instantly accessible, fully documented records
One site manager commented:
"flowdit has not only improved our efficiency but also strengthened our team spirit. Everyone sees how their work contributes to better outcomes, and that motivates us to keep improving."
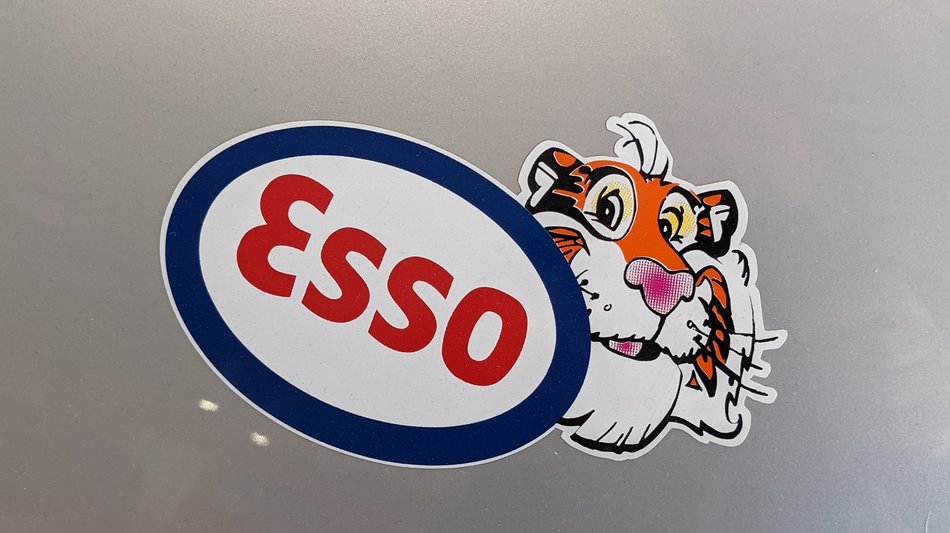
From Static Checklists to Operational Intelligence
One of the most significant shifts has been in the use of frontline data. Previously, observations were collected in isolation, often buried in folders or Excel sheets, rarely used beyond the moment.
With flowdit, that data now powers a cycle of continuous improvement. Custom dashboards enable leadership to spot trends in real time: such as recurring equipment failures or gaps in procedural adherence, and respond with targeted interventions.
For instance, when food safety checks at select sites revealed inconsistencies, EG Group retrained specific teams and adjusted digital workflows to include enhanced guidance. What once required a top-down audit cycle now happens within days, driven by real-time operational intelligence.
Culture Change: Enabling Every Level of the Organization
Beyond technology, the shift to flowdit marks a deeper transformation in culture. Frontline staff now have tools that are easy to use and meaningful to their daily routines. Managers are freed from micromanagement and can focus on coaching and strategy.
Adoption has been swift: the mobile platform required minimal training, and hundreds of sites were onboarded in phases without operational disruption. The no-code environment means internal teams can continuously adjust workflows without external consultants or software development.
This flexibility enables EG Group to rapidly align operations with new food concepts, compliance regulations, or regional rollouts, modifying processes in hours, not weeks.
Scaling the Vision: Toward a Unified Operational Ecosystem
Building on the success of its frontline digitization, EG Group now plans to expand flowdit into adjacent areas such as:
Contractor oversight
Maintenance management
Supply chain quality control
The goal is a single connected ecosystem, where everyone, from employees to external partners, operates on the same digital foundation. The benefits go beyond efficiency: they extend to safety, agility, and customer satisfaction.
As one operations director put it:
"We used to spend time chasing problems. Now, we're designing systems that prevent them."
About EG Group
EG Group is a global leader in fuel and convenience retail, operating thousands of branded retail sites in Europe, North America, and the Asia-Pacific region. With a multi-format approach combining petrol stations, grocery offerings, foodservice and quick-service restaurants, EG Group is committed to delivering convenient, high-quality experiences to customers every day. The company partners with globally recognized brands including Esso, KFC, SPAR, and Starbucks to bring best-in-class offerings to every location.
About flowdit
flowdit is a Connected Operations Platform built to simplify frontline work in complex operational environments. From inspections and maintenance to compliance and quality assurance, flowdit replaces paper and spreadsheets with intuitive digital workflows, real-time data capture, and seamless collaboration across sites. Leading organizations across manufacturing, retail, construction, and energy use flowdit to drive productivity, compliance, and continuous improvement.
For more information: https://flowdit.com
Media Contact
Daniela Reis
Head of Communications
flowdit - Operational Excellence
Email: press@flowdit.com
Phone: +49 131 94509 00
SOURCE: flowdit
View the original press release on ACCESS Newswire